I pavimenti resilienti
Resilient coatings
- 04 Set 2022
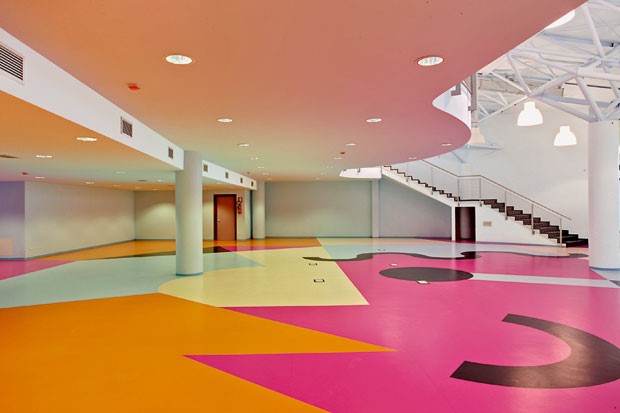
Per rivestimenti resilienti si intendono dei prodotti caratterizzati da una maggiore flessibilità rispetto ai cosiddetti “materiali duri”. Questi materiali, se sottoposti ad una pressione sulla superficie, hanno la proprietà, detta appunto resilienza, di deformarsi in maniera flessibile per effetto di sollecitazioni di breve durata, e di riassumere rapidamente la configurazione iniziale al termine della sollecitazione. la deformazione può diventare permanente se il carico è continuo e costante.
Fa parte di questa famiglia un elevato numero di prodotti diversificati secondo tre tipologie: gomma, linoleum e vinilici. questi prodotti sono presenti sul mercato in teli e/o in quadrotte.
i rivestimenti resilienti presentano specifiche caratteristiche:
- Caratteristiche prestazionali: flessibilità, elasticità permanente, impermeabilità, resistenza, pulibilità, calore al tatto, confortevolezza al passo, isolamento ai rumori d’impatto (abbattimento fino a 20 db), resistenza termica confrontabile con il legno e la moquette, buona resistenza all’usura, alle macchie e all’acqua, bassa conduttività elettrica.
- Caratteristiche applicative: questi materiali sono molto leggeri (da 1 a 6 kg/m2), maneggevoli, adattabili a qualsiasi geometria (sono facilmente tagliabili), e pertanto si distinguono anche per la facilità di applicazione.
Queste tipologie di rivestimenti sono solitamente utilizzate per la realizzazione di aeroporti, uffici, negozi, palestre, stabilimenti industriali, autobus, treni e navi, cliniche ed ospedali, scuole e asili, situazioni quindi dove la pulibilità, l’igiene e il comfort delle superfici rivestono un ruolo di primaria importanza ma, allo stesso tempo, dove le superfici sono soggette a traffico intenso e utilizzo continuo.
Le precauzioni di posa dei materiali resilienti sono sensibilmente differenti rispetto a quelle di altri materiali da rivestimento. devono essere infatti considerate alcune caratteristiche legate alla natura stessa di questi materiali:
- Deformabilità: la pavimentazione resiliente è di norma deformabile pertanto, sottoposta ad un carico concentrato, non è in grado di ridistribuire la sollecitazione ma la trasferisce puntualmente sul sottofondo che deve, quindi, avere elevate caratteristiche prestazionali (in particolare in termini di resistenza meccanica e resistenza all’abrasione)
- Basso spessore: lo spessore di pochi millimetri rende le pavimentazioni resilienti adatte alla posa dove le quote di progetto non permettono la posa di altre tipologie di rivestimento. al contempo il basso spessore non permette di nascondere irregolarità del fondo di posa. per questo è sempre necessaria un’adeguata preparazione delle superfici con specifici prodotti liscianti. per rivestimenti particolarmente sottili anche la scelta dell’adesivo è importante in quanto una viscosità alta può portare a difetti estetici sulla superficie del rivestimento (le righe dell’adesivo possono essere visibili sulla pavimentazione finita).
- Resilienza: la caratteristica resilienza di questi materiali aiuta ad aumentare le prestazioni di isolamento acustico e la resilienza agli urti. la tendenza del materiale a riassumere la configurazione iniziale ne rende però difficile la posa in corrispondenza di curve o spigoli vivi. in questi casi la posa deve essere effettuata utilizzando adesivi con forte presa iniziale (adesivi a contatto o bande adesive) che impediscano il ritorno elastico del materiale, così da evitare il distacco del rivestimento dagli angoli. allo stesso tempo i materiali in teli, confezionati in rotoli, tendono a mantenere la memoria dell’imballo e devono perciò essere disimballati alcuni giorni prima della posa in modo da riassumere la loro conformazione iniziale.
- Stabilità dimensionale: alcuni materiali resilienti possono subire delle variazioni dimensionali quando vengono sottoposti a forti gradienti termici. se questa caratteristica non viene valutata adeguatamente in fase di scelta dell’adesivo per la posa è possibile incorrere in problematiche di puntamento o apertura delle giunte. in questi casi è quindi necessario scegliere adesivi che siano in grado di bloccare i movimenti del rivestimento assicurando la durabilità della messa in opera. spesso questo fenomeno è legato alla metodologia di produzione (per calandratura) e il fabbricante riporta sui materiali una direzione preferenziale di posa per renderlo meno influente.
Alcune caratteristiche dei rivestimenti resilienti rendono necessarie particolari accortezze in fase di posa per evitare il manifestarsi di difetti successivi alla messa in opera:
- Impermeabilità del rivestimento: tale caratteristica rende necessaria la verifica dell’asciugamento del supporto prima di procedere alla posa per evitare la formazione di bolle sulla superficie. oltre alla presenza di umidità di risalita dal supporto, tale difetto si può manifestare per altri due motivi. il primo è legato ad una non sufficiente massaggiatura finale del rivestimento che, al termine della posa, deve essere passato con rullo dal centro verso i bordi per eliminare eventuali bolle d’aria intrappolate durante la stesura dei teli o delle piastre. il secondo è legato ad errori in fase di messa in opera: la pavimentazione posata non deve essere sottoposta ad alcun carico fino alla pedonabilità dell’adesivo. in caso contrario il carico potrebbe provocare uno spostamento localizzato dell’adesivo fresco e quindi, a presa avvenuta, una mancata adesione con conseguente formazione di bolle.
- Elevata resistenza all’usura: i materiali resilienti sono molto resistenti anche in ambienti soggetti a traffico intenso. Per riuscire a garantire la durabilità è però necessaria un’appropriata scelta dell’adesivo, in funzione delle condizioni di esercizio. in particolar modo nel caso in cui siano previsti lavaggi frequenti o permanenza di acqua sulle superfici (e non sia prevista la sigillatura o saldatura dei giunti) è necessario evitare l’utilizzo di adesivi in dispersione ed orientarsi verso la scelta di adesivi reattivi per non incorrere in dilavamenti o rapido degrado dello strato adesivo con conseguente distacco del rivestimento.
Per essere idonei alla posa di un rivestimento resiliente i supporti devono soddisfare specifici requisiti, variabili a seconda della destinazione d’uso prevista.
SPESSORE DEL SUPPORTO
Nel caso di posa di rivestimenti resilienti è sempre consigliabile la realizzazione di massetti desolidarizzati, assicurando il posizionamento (o verificando la presenza nel caso di massetti esistenti) di un’idonea barriera al vapore (ad es. fogli di polietilene dello spessore di almeno 0,3 mm, sormontati e nastrati) che impedisca la possibile risalita d’umidità dagli strati sottostanti. la necessità di una barriera al vapore è legata al fatto che i rivestimenti resilienti vengono a creare una superficie impermeabile: è quindi fondamentale verificare che il supporto sia esente da problematiche di risalita di umidità al fine di evitare distacchi e formazione di bolle. lo spessore minimo del massetto desolidarizzato deve essere di almeno 4 cm (con eventuali aumenti da valutarsi in funzione della natura del sottofondo e dai carichi previsti in esercizio). Lo spessore deve essere valutato anche in relazione alla presenza di strati di materiale comprimibile o di tubazioni (sempre almeno 2,5 cm sopra tubazioni passanti per evitare cedimenti localizzati. Poichè in generale i pavimenti resilienti, per la loro natura, non sono in grado di distribuire i carichi a cui saranno sottoposti, la loro affidabilità e durata dipenderanno, in larga misura, dalle caratteristiche meccaniche e dal grado di finitura del loro supporto, costituito dal massetto oltre che dalla rasatura, che dovranno quindi garantirne la resistenza ai carichi di esercizio previsti, anche puntuali, senza il rischio di cedimenti.
RESISTENZA MECCANICA E COMPATTEZZA
La resistenza meccanica dovrà essere valutata in funzione delle condizioni di esercizio del rivestimento e della sua destinazione d’uso. indicativamente si ritiene adeguata una resistenza di 20 MPa per un sottofondo in ambiente civile, che deve essere incrementata a 30 MPa nel caso di ambiente commerciale/industriale. poiché nella maggior parte delle situazioni il sottofondo deve essere lisciato prima di effettuare la posa, anche i prodotti scelti per effettuare la lisciatura devono soddisfare requisiti di resistenza meccanica di 20-25 Mpa.
Un aiuto alla scelta dei prodotti idonei al raggiungimento delle corrette resistenze è la norma “UNI EN 13813 – materiali per massetti e massetti” che permette una precisa classificazione dei prodotti per la realizzazione dei massetti e delle lisciature in termini di resistenza meccanica a compressione, a flessione e anche di resistenza al fuoco.
Nel caso in cui il supporto esistente non abbia le caratteristiche di resistenza meccanica richieste, è possibile valutare se procedere ad un consolidamento, mediante l’applicazione di prodotti idonei come:
- primer epossidici bicomponenti, seguiti da spaglio di quarzo
- primer poliuretanico monocomponente, seguiti da spaglio di quarzo
STAGIONATURA
Prima di procedere alla posa il supporto deve essere adeguatamente stagionato. Il tempo di stagionatura per i sottofondi cementizi tradizionali in sabbia e cemento è da considerare pari a circa 7-10 giorni per centimetro di spessore. Nell’arco di questo tempo massetti ed intonaci sono soggetti ad un ritiro igrometrico che può portare alla formazione di fessurazioni; la posa effettuata senza rispettare le corrette tempistiche, quindi, può portare al rischio di trasferimento di tali fessurazioni sul rivestimento con conseguente possibile distacco e sollevamento del rivestimento. se poi la posa viene realizzata prima del completo asciugamento si può verificare la formazione di bolle sulla superficie.
I tempi possono essere opportunamente ridotti utilizzando leganti o malte premiscelate a ritiro controllato e ad asciugamento veloce o rapido a presa ed asciugamento rapidi (24 ore), a ritiro controllato, di classe Ct-C60-F10-a1fl secondo EN 13813.
L’utilizzo delle malte premiscelate, rispetto alla realizzazione di un massetto tradizionale, offre i seguenti vantaggi:
- permette di risolvere il problema, comune a molte aree, del difficile reperimento di aggregati di corretta granulometria e di buona qualità.
- permette di evitare errori nei dosaggi e problemi legati alla qualità della manodopera.
- è la soluzione ottimale laddove vi sono difficoltà di stoccaggio della materie prime (inerti, cemento, ecc.), ad esempio negli interventi di ristrutturazione nei centri storici.
- garantisce tempi di asciugamento e di stagionatura ridotti, indipendenti dalla variabilità degli inerti reperibili in cantiere, da errori di dosaggio o dalla qualità della manodopera ed è quindi particolarmente consigliato nel caso di posa di pavimenti sensibili all’umidità come i pavimenti resilienti.
- grazie all’obbligatorietà della marcatura Ce di questa tipologia di prodotti, in accordo alla norma UNI EN13813, permette di conoscere a priori quali saranno le prestazioni meccaniche finali del massetto.
ASCIUGATURA
Per tutte le tipologie di rivestimento resiliente è estremamente importante valutare che il supporto sia asciutto prima di procedere alla posa. la valutazione dell’asciugamento deve essere effettuata mediante l’utilizzo di igrometro: per poter procedere alla posa l’umidità residua deve essere inferiore a 2,5-3% per supporti cementizi, inferiore a 0,5% per supporti a base di gesso o anidrite. i valori più affidabili si ottengono effettuando la misurazione con igrometro al carburo, in alternativa è possibile utilizzare igrometri elettrici.
Nel caso in cui l’umidità sia leggermente superiore ai valori sopra indicati e non sia possibile attendere ulteriormente per consentire l’evaporazione dell’acqua in eccesso, si può intervenire applicando prima della posa, e sempre prima della messa in opera del livellante, un primer o teli impermeabilizzanti anche se adottando il sistema con i teli sistema il pavimento sarà assimilabile ad una pavimentazione flottante, pertanto non sarà idoneo nel caso di traffico pesante (es. passaggio di automobili o carrelli elevatori).
PULIZIA
Le superfici su cui si effettua la posa devono essere adeguatamente pulite ed esenti da polvere, grassi, oli, pitture, materiali in fase di distacco o qualsiasi altra sostanza che possa compromettere l’adesione.
FESSURAZIONI
Qualsiasi fessurazione presente deve essere adeguatamente sigillata prima di procedere alla messa in opera del rivestimento utilizzando prodotti idonei. La mancata sigillatura delle fessurazioni può dare origine a distacchi e a bolle superficiali.
PLANARITA’
I resilienti sono rivestimenti molto sottili per i quali è richiesta una assoluta regolarità del supporto: qualsiasi imperfezione o un supporto non perfettamente planare potrebbero trasparire anche sulla superficie rivestita. La superficie di posa dovrà quindi essere piana e ad una quota inferiore al piano finito pari allo spessore del pavimento, dell’adesivo e dell’eventuale strato di regolarizzazione o rasatura. La tolleranza di planarità normalmente ammessa, che sostanzialmente corrisponde a quella del pavimento finito, misurata sotto un regolo metallico di 3 m, è indicata in 6 mm. L’eliminazione delle ruvidità superficiali ed eventuali piccole correzioni della planarità saranno realizzate prima della posa mediante l’impiego di prodotti idonei. Inoltre tutti i supporti devono essere primerizzati con idoneo promotore di adesione prima dell’applicazione del livellante.
TIPOLOGIE DI ADESIVI PER RESILIENTI
Gli adesivi per resilienti si possono dividere nelle seguenti categorie:
- Adesivi in emulsione (acquosa): si tratta di adesivi tendenzialmente esenti da sostanze nocive, caratterizzati da una viscosità tale da facilitarne la stesura, a seguito della quale si prescrive un tempo d’attesa, necessario per aumentarne il tiro, prima della posa del rivestimento.
- Adesivi in solvente: per questi adesivi il solvente fornisce una viscosità tale da facilitare la stesura e la sua rapida evaporazione conferisce a questi prodotti un tempo di attesa relativamente breve prima di poter procedere alla posa del rivestimento.
- Adesivi reattivi: si tratta diadesivi a base diresine reattive, principalmente poliuretaniche o epossi-poliuretaniche, idonei all’incollaggio anche su supporti non assorbenti o dove siano richieste caratteristiche di adesione particolarmente elevate (es. superfici sottoposte a traffico intenso).
- Adesivi policloroprenici (a contatto): si tratta di adesivi con o senza solvente, da applicare in doppia spalmatura, caratterizzati da una presa immediata dopo l’accoppiamento dei materiali e quindi idonei alla posa di rivestimenti su superfici curve (sgusce) o su spigoli (generalmente arrotondati) e di profili preformati (zoccolini battiscopa, paragradini, angolari, ecc.).
- Nastri biadesivi: in alternativa all’uso di adesivi a contatto sono disponibili sul mercato anche bande biadesive armate a base acrilica, idonee alla posa di profili, sgusce o rivestimenti ove sia richiesta una presa immediata.
CARATTERISTICHE DEL RIVESTIMENTO
I rivestimenti resilienti sono commercializzati, a seconda del materiale, in teli o in quadrotte. Per quanto riguarda i materiali venduti in teli, se conservati a lungo in rotoli, si possono verificare dei problemi legati alla tendenza del rivestimento a mantenere una leggera deformazione dovuta all’imballo, soprattutto a basse temperature, per questo motivo è sempre consigliato disimballare e srotolare i rivestimenti alcuni giorni prima della posa, così da eliminare la “memoria” legata al loro confezionamento.
Quando tali tensioni non vengano eliminate prima della posa, o per rivestimenti particolarmente rigidi, può manifestarsi la tendenza del rivestimento a sollevarsi non appena venga liberato dalla pressione esercitata al momento della posa. in questi casi è opportuno usare adesivi a forte adesività (tack) iniziale.
Oltre ai problemi di confezionamento, per alcuni prodotti ci sono problematiche intrinseche di stabilità dimensionale, legate principalmente alle modalità di produzione. Le norme UNI per i pavimenti vinilici e di gomma stabiliscono in tal senso che la variazione dimensionale dei materiali liberi (non incollati) dopo esposizione al calore non debba superare lo 0,3 % per le piastrelle e lo 0,4 % per i teli. Le variazioni possono essere sia positive che negative e generalmente sono diverse se rilevate longitudinalmente o trasversalmente al senso di calandratura. La scelta dell’adesivo deve essere migliorativa in termini di stabilità, tanto da portare i limiti a quanto indicato dalla norma EN 14259.
Se il prodotto per la posa non viene scelto correttamente si genera nel film di adesivo un’eccessiva tensione che può dare origine ai seguenti difetti:
- piastrelle o teli che puntano sulle giunte
- giunti che si aprono
- distacchi dovuti a fessurazioni del film di adesivo o a rottura del supporto.
Per ovviare a queste problematiche è necessario verificare sempre la solidità del supporto e scegliere un adesivo compatibile con il rivestimento, che abbia quindi una buona capacità di bloccare il materiale e un’adeguata elasticità dopo la presa. Anche per limitare problemi legati alla stabilità dimensionale è importante:
- lasciare il rivestimento libero dall’imballo ad “acclimatarsi” nei locali dove dovrà essere posato affinché assuma la stabilità dimensionale relativa alle condizioni termoigrometriche del luogo;
- posare il rivestimento a condizioni termoigrometriche intermedie rispetto alle escursioni cui sarà sottoposto (15°C<t<30°C).
Fonti
Quaderno Tecnico MAPEI – LA POSA DEI RIVESTIMENTI RESILIENTI
Ing. Paolo Croce – ZEDPROGETTI srl
Resilient coatings are products with greater flexibility than so-called “hard materials”. When subjected to surface pressure, these materials have the property, called resilience, of flexibly deforming due to short-lived stresses, and of quickly summarising the initial configuration at the end of the stress.
This family includes a large number of products diversified into three types: rubber, linoleum and vinyl. these products are present on the market in sheets and / or squares.
resilient coatings have specific characteristics:Performance characteristics: flexibility, permanent elasticity, impermeability, resistance, cleanability, warmth to the touch, comfort to the step, insulation to impact noises (abatement up to 20 db), thermal resistance comparable with wood and carpeting, good resistance to wear, stains and water, low electrical conductivity.
Application characteristics: these materials are very light (from 1 to 6 kg/m2), easy to handle, adaptable to any geometry (they are easily cut), and therefore also stand out for the ease of application.
These types of coatings are usually used for the construction of airports, offices, shops, gyms, industrial plants, buses, trains and ships, clinics and hospitals, schools and kindergartens, so situations where cleanability, hygiene and comfort of surfaces play a role of primary importance but, at the same time, where the surfaces are subject to heavy traffic and continuous use.The installation precautions for resilient materials are significantly different from those of other coating materials:
Deformability: resilient flooring is normally deformable, therefore, when subjected to a concentrated load, it is not able to redistribute the stress but transfers it punctually to the substrate, which must therefore have high performance characteristics (in particular in terms of mechanical resistance and resistance to abrasion).
Low thickness: the thickness of a few millimetres makes the floor resilient suitable for installation where the project dimensions do not allow the installation of other types of coating. at the same time, the low thickness does not allow to hide irregularities in the laying surface. for this reason it is always necessary to prepare the surfaces with specific smoothing products. for particularly thin coatings even the choice of adhesive is important because a high viscosity can lead to aesthetic defects on the surface of the coating (the lines of the adhesive can be visible on the finished floor).
Resilience: the characteristic resilience of these materials helps to increase the acoustic insulation performance and the impact resistance. the tendency of the material to summarize the initial configuration makes it difficult to lay it on curves or sharp edges. in these cases, laying must be carried out using adhesives with a strong initial setting (contact adhesives or adhesive strips) that prevent the material from returning elastically, so as to prevent the coating from detaching from the corners. at the same time, sheet materials, packaged in rolls, tend to maintain the memory of the packaging and must therefore be unpacked a few days before laying in order to summarise their initial shape.
Dimensional stability: some resilient materials may undergo dimensional variations when subjected to high thermal gradients. if this characteristic is not adequately evaluated when choosing the adhesive for installation, problems may arise in terms of pointing or opening the joints. in these cases, it is therefore necessary to choose adhesives that are able to block the movements of the coating, ensuring the durability of the installation. often this phenomenon is linked to the production method (by calendering) and the manufacturer reports on the materials a preferred direction of installation to make it less influential.
Some characteristics of resilient coatings require special care during installation to avoid the appearance of defects after installation:Waterproofing of the cladding: this characteristic makes it necessary to check that the substrate is dry before laying to avoid the formation of bubbles on the surface. in addition to the presence of rising damp from the substrate, this defect may occur for two other reasons. the first is linked to insufficient final massaging of the cladding which, at the end of laying, must be passed with a roller from the centre to the edges to eliminate any air bubbles trapped during the laying of the sheets or plates. The second is related to errors during installation: the installed floor must not be subjected to any load until the adhesive can be walked on. Otherwise, the load could cause a localized displacement of the fresh adhesive and then, after setting, a lack of adhesion with consequent formation of bubbles.
High wear resistance: resilient materials are very resistant even in environments subject to heavy traffic. In order to guarantee durability, however, an appropriate choice of adhesive is necessary, depending on the operating conditions. especially in cases where frequent washing or permanence of water on the surfaces is required (and where the sealing or welding of the joints is not required), it is necessary to avoid the use of dispersion adhesives and move towards the choice of reactive adhesives so as not to run into washouts or rapid deterioration of the adhesive layer with consequent detachment of the coating.
To be suitable for the installation of a resilient coating, the substrates must meet specific requirements, which vary according to the intended use.THICKNESS OF THE SUBSTRATE
When laying resilient coatings, it is always advisable to make desolidarized screeds, ensuring the positioning (or checking the presence in the case of existing screeds) of a suitable vapour barrier (e.g. polyethylene sheets at least 0.3 mm thick, overlapped and taped) that prevents the possible rise in humidity from the layers below. the need for a vapour barrier is linked to the fact that the resilient coatings create an impermeable surface: it is therefore essential to check that the substrate is free from problems of rising damp in order to avoid detachment and formation of bubbles. the minimum thickness of the desolidarised screed must be at least 4 cm (with any increases to be evaluated according to the nature of the substrate and the expected loads in use). The thickness must also be evaluated in relation to the presence of layers of compressible material or pipes (always at least 2.5 cm above passing pipes to avoid localised subsidence. Since resilient floors, by their nature, are generally unable to distribute the loads to which they will be subjected, their reliability and durability will depend, to a large extent, on the mechanical characteristics and degree of finish of their support, consisting of the screed as well as the shaving, which must therefore ensure the resistance to the expected operating loads, even punctual, without the risk of failure.MECHANICAL RESISTANCE AND COMPACTNESS
The mechanical resistance must be evaluated according to the operating conditions of the coating and its intended use. indicatively, a resistance of 20 MPa is considered appropriate for a subfloor in a civil environment, which must be increased to 30 MPa in the case of a commercial/industrial environment. since in most situations the subfloor must be smoothed before laying, even the products chosen to perform the smoothing must meet mechanical resistance requirements of 20-25 MPa.
An aid to the choice of products suitable for achieving the correct strengths is the standard “UNI EN 13813 – materials for screeds and screeds” which allows a precise classification of products for the production of screeds and smoothing in terms of mechanical resistance to compression, bending and also fire resistance.
If the existing support does not have the required mechanical resistance characteristics, it is possible to assess whether to proceed to a consolidation, by applying suitable products such as:two-component epoxy primer, followed by quartz coating
single-component polyurethane primer, followed by quartz coatingMATURING
Before laying, the substrate must be properly cured. The curing time for traditional cementitious substrates made of sand and cement is about 7-10 days per centimetre of thickness. During this time, screeds and plasters are subject to hygrometric shrinkage, which can lead to the formation of cracks; laying without respecting the correct timing, therefore, can lead to the risk of transferring these cracks onto the cladding with consequent possible detachment and lifting of the cladding. if the laying is then carried out before complete drying, the formation of bubbles on the surface can occur.
The times can be suitably reduced by using binders or pre-mixed mortars with controlled shrinkage and fast or rapid drying with rapid setting and drying (24 hours), with controlled shrinkage, of class Ct-C60-F10-a1fl according to EN 13813.The use of pre-mixed mortars, compared to the production of a traditional screed, offers the following advantages:
allows to solve the problem, common to many areas, of the difficulty of finding aggregates of correct grain size and good quality.
The use of this technology allows to avoid errors in the dosages and problems related to the quality of the manpower.
is the optimal solution where there are difficulties in storing raw materials (aggregates, cement, etc..), for example in restructuring interventions in historic centers.
The system guarantees short drying and curing times, independent of the variability of the aggregates available on site, errors in dosage or the quality of the workforce, and is therefore particularly recommended in the case of the installation of moisture-sensitive floors such as resilient floors.
Thanks to the mandatory CE marking of this type of product, in accordance with UNI EN13813, it is possible to know in advance what the final mechanical performance of the screed will be.DRYING
For all types of resilient coating, it is extremely important to assess that the substrate is dry before laying. the drying must be assessed using a hygrometer: to be able to proceed with laying, the residual humidity must be less than 2.5-3% for cementitious substrates, less than 0.5% for gypsum-based or anhydrite substrates. the most reliable values are obtained by carrying out the measurement with a carbide hygrometer, alternatively, electric hygrometers can be used.If the humidity is slightly higher than the values indicated above and it is not possible to wait any longer to allow the excess water to evaporate, it is possible to apply a waterproofing primer or sheets before laying, and always before laying the levelling agent, even if adopting the system with the system sheets the floor will be similar to a floating floor, therefore it will not be suitable for heavy traffic (e.g. passage of cars or forklifts).
CLEANING
The surfaces on which the tiles are to be laid must be properly cleaned and free of dust, grease, oil, paint, detaching materials or any other substance that could compromise adhesion.SLOTS
Any cracks present must be properly sealed before proceeding with the installation of the coating using suitable products. Failure to seal cracks can result in detachment and surface bubbles.FLATNESS
Resilient coatings are very thin coatings for which an absolute regularity of the support is required: any imperfection or a support that is not perfectly flat could also appear on the coated surface. The laying surface must therefore be flat and at a level lower than the finished surface equal to the thickness of the floor, the adhesive and any levelling or levelling layer. The normally permitted flatness tolerance, which essentially corresponds to that of the finished floor, measured under a metal rule of 3 m, is indicated in 6 mm. The removal of surface roughness and any minor corrections to the flatness will be carried out before laying using suitable products. In addition, all substrates must be primed with a suitable adhesion promoter before applying the levelling agent.TYPES OF ADHESIVES FOR RESILIENTS
Resilient adhesives can be divided into the following categories:Emulsion adhesives (watery): these adhesives tend to be free of harmful substances, characterized by a viscosity that facilitates the application, after which a waiting time is prescribed, necessary to increase the pull, before the laying of the coating.
Solvent adhesives: for these adhesives the solvent provides a viscosity that facilitates the application and its rapid evaporation gives these products a relatively short waiting time before proceeding with the laying of the coating.
Reactive adhesives: these are diadhesive adhesives based on reactive resins, mainly polyurethane or epoxy-polyurethane, suitable for gluing even on non-absorbent substrates or where particularly high adhesion characteristics are required (e.g. surfaces subject to heavy traffic).
Polychloroprene adhesives (in contact): these are adhesives with or without solvent, to be applied in double coating, characterized by an immediate setting after the coupling of the materials and therefore suitable for laying coatings on curved surfaces (shells) or on edges (generally rounded) and preformed profiles (skirting boards, nosing, corners, etc.).
Double-sided adhesive tapes: as an alternative to the use of contact adhesives, double-sided reinforced acrylic-based strips are also available on the market, suitable for laying profiles, shells or coverings where immediate setting is required.CHARACTERISTICS OF THE COATING
Resilient coatings are marketed, depending on the material, in sheets or tiles. As for the materials sold in sheets, if stored for a long time in rolls, there may be problems related to the tendency of the coating to maintain a slight deformation due to packaging, especially at low temperatures, for this reason it is always recommended to unpack and unroll the coatings a few days before laying, so as to eliminate the “memory” related to their packaging.
When these tensions are not eliminated before laying, or for particularly rigid coatings, the tendency of the coating to rise as soon as it is released from the pressure exerted at the time of laying may occur. in these cases it is advisable to use adhesives with strong initial tack.In addition to packaging problems, for some products there are intrinsic problems of dimensional stability, mainly linked to production methods. The UNI standards for vinyl and rubber floors establish in this sense that the dimensional variation of free materials (not glued) after exposure to heat must not exceed 0.3 % for tiles and 0.4 % for sheets. The variations can be both positive and negative and are generally different if measured longitudinally or transversely to the direction of calendering. The choice of the adhesive must be improved in terms of stability, so as to bring the limits to those indicated in EN 14259.
If the product for laying is not chosen correctly, excessive tension is generated in the adhesive film, which can give rise to the following defects:
tiles or sheets that point to the joints
joints that open
detachments due to cracks in the adhesive film or breakage of the substrate.
To avoid these problems it is necessary to always check the solidity of the support and choose an adhesive compatible with the coating, which therefore has a good capacity to block the material and adequate elasticity after setting. It is also important to limit problems related to dimensional stability:leave the covering free from the packaging to “acclimatize” in the rooms where it must be laid so that it assumes the dimensional stability relative to the thermo-hygrometric conditions of the place;
Lay the cladding at intermediate thermohygrometric conditions with respect to the excursions to which it will be subjected (15°C<t<30°C).